Q.E.D. – Making Moulds
from Silicon
by Thorsten Wieking
A short while ago, someone asked on rec.models.scale if silicon
(the one used to seal kitchen sinks and bath tubs) could be used to make
moulds. Since I have a bottle of the said silicon, I've done a few tests
myself. Following the KISS principle (Keep it Simple and Stupid), I planned
a one-sided mould with an open rear.
For testing purposes I used a variety of half-forms, such as bombs, bergens,
and drop tanks. First I fixed them with white glue to a flat surface,
in this case a flat piece of clear plastic. Because these parts have a
very flat surface, I didn't coat them with Vaseline to help get them out
of the mould later.
Next I covered the parts with silicon, paying attention to cover every
part of the test objects. Because this type of silicon is very thick,
you have to paste it onto the parts rather than letting it flow.
Keeping the outer surface of the mould flat helps you later when filling
the mould cavity with your casting material. I tried to keep the layers
thin enough so they can dry within a day but be stable enough for casting.
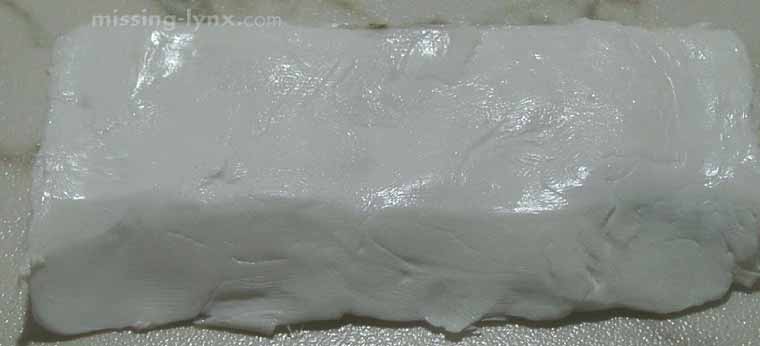
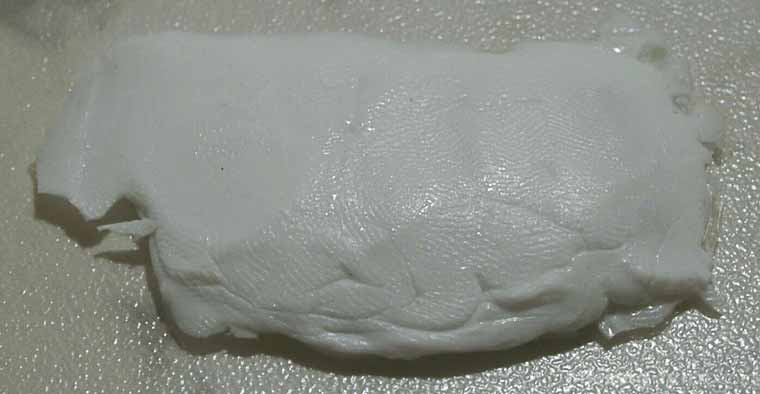
After a drying time of approximately one day, I removed the parts from
the now dry silicon.
To make it even cheaper, I filled the moulds with Miliput putty, making
sure that I pressed them hard enough into the mould to capture the smallest
details. This is where the flat outside of the mould comes into play,
as this helps in filling the mould with Miliput.
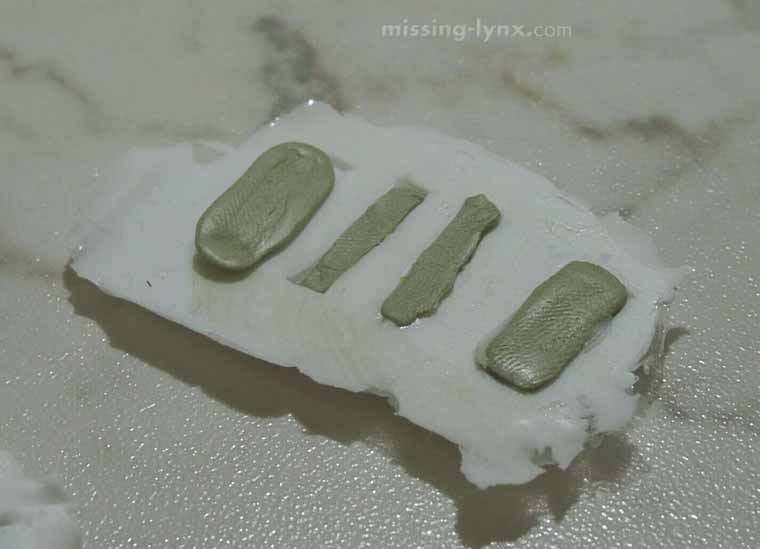
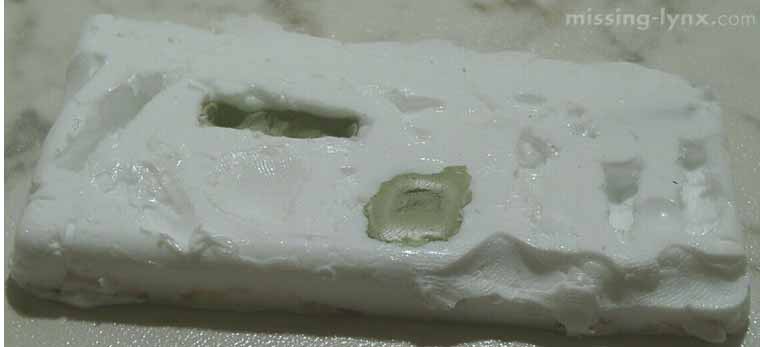
After the Miliput had cured, I removed the parts with the following results:
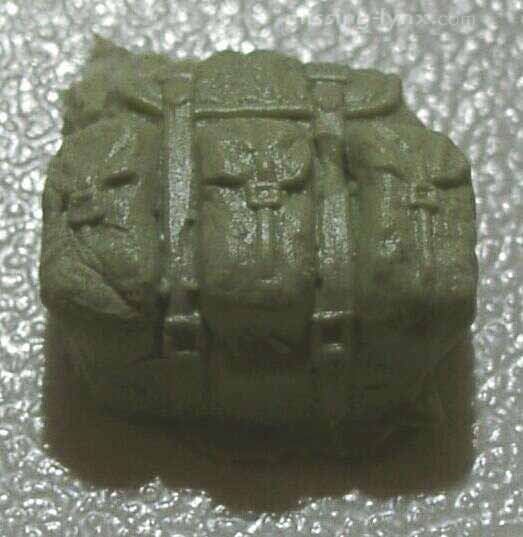
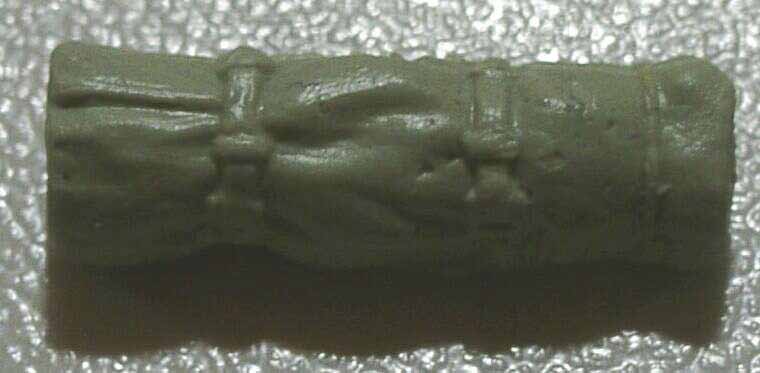
The moulding process could be improved by using clear silicon, giving
you visual control over how the silicon flows around the part.
In conclusion: for 5 Euros for 300 ml Silicon, and around 5 Euros for
Yellow Miliput, the total cost should be in the region of 10 Euros in
total. Compare that with the usual costs of resin and silicon! If you
only require a small mould for a limited number of objects, such as a
few more bergens or tarps, this technique could be a convenient alternative
for you.
Thorsten Wieking, 2002
|